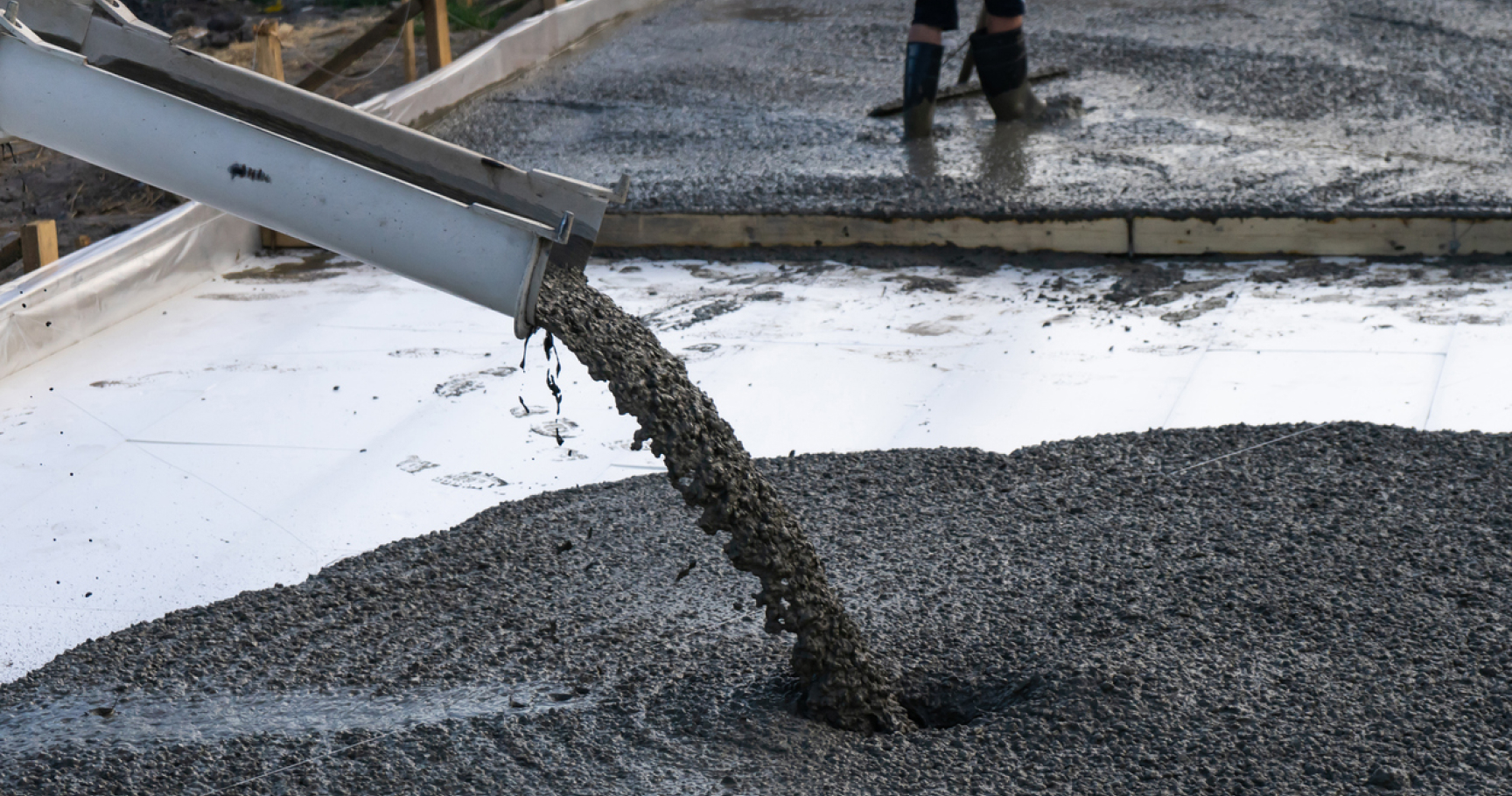
Premium Materials for
High-Quality Concrete Projects
Metheny has the premium materials that form the backbone of our high-quality concrete solutions. From the finest aggregates to advanced admixtures, our carefully selected materials ensure durability, strength, and reliability in every project. Explore our commitment to excellence and see how our top-tier materials contribute to superior concrete performance.
Type I/II Cement
Overview of ASTM C 50 Type I/II Cement
ASTM C 50 Type I/II Cement carries a dual designation, meaning it satisfies the standards for either Type I or Type II Cement. The American Society for Testing and Materials (ASTM) oversees these specifications. ASTM C 50 specifically addresses the standards for physical tests, including sampling, sample preparation, packaging, and marking of lime and limestone products.
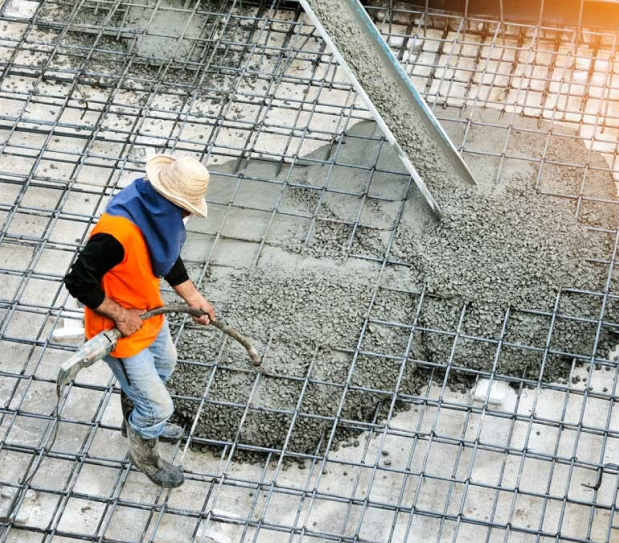
Applications of Type I Cement
Type I cement is formulated for general construction purposes where no special properties are specifically required. It is commonly used in the construction of buildings, bridges, pavements, precast units, and other standard structures. This type of cement is chosen for its versatility and reliability in typical construction scenarios.
Applications and Importance of
Type II Cement
Type II cement is tailored for use in environments that require moderate sulfate resistance or moderate heat of hydration. It is essential for structures in contact with soils or waters that contain sulfate ions. Type II cement helps prevent the concrete from severe damage such as expansion and cracking, which are common issues when sulfate attacks occur. This characteristic makes Type II cement critical for maintaining the durability and integrity of exposed structures.
Chemical Admixture
Chemical Admixture
Admixtures, which can be natural or manufactured chemicals, are added to concrete before or during mixing. They are vital in challenging construction conditions, such as extreme temperatures, specific pumping needs, or requirements for early-age strength. Admixtures enhance the workability of fresh concrete and improve the durability of hardened concrete.
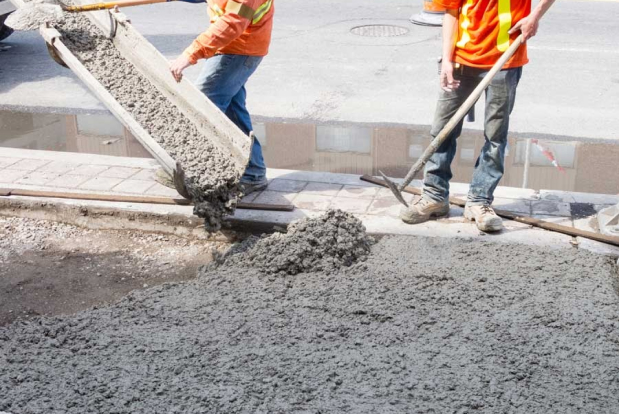
There are a few chemical admixtures that are most commonly used:
- Air-Entraining Admixtures: Used in exterior pours to withstand freezing and thawing cycles.
- Water Reducer Admixtures: These lower the water content in fresh concrete, increasing its strength and allowing for a higher slump without additional water.
- High Range Water Reducers (HRWR): Ideal for producing high-strength, high-performance concrete.
- Retarders: Applied in large pours or on hot days to delay the initial setting of concrete by more than an hour.
- Accelerators: Used in cold weather to reduce the initial setting time and achieve higher early strength.
Concrete Sand
Concrete Sand
Using sand in concrete not only reduces costs but also limits shrinkage as the concrete cures. Concrete sand, a fine aggregate, is crucial for filling voids between the coarser aggregates. It is produced by crushing rocks at the quarry, then washed to remove any large pieces, ensuring a consistent quality.
The right mix of coarse aggregate, sand, and cement is essential for creating a strong and durable concrete mix. This balance is crucial, as it enhances the structural integrity and longevity of the concrete, ensuring it can withstand environmental stresses and resist cracking.
Flowable-Fill
Controlled Low-Strength Material (CLSM)/Flowable Fill
Flowable fill, also known as Controlled Low-Strength Material (CLSM), is a versatile, self-compacting cementitious material known for its self-leveling, non-corrosive properties, and quick set time. It is commonly used as backfill, structural fill, and for filling abandoned underground facilities such as storage tanks, tunnel shafts, and sewers.
The material is favored for its safety, ease of placement, and compaction, offering economic advantages by reducing labor and time on projects. Flowable fill provides reliable, maintenance-free results, preventing settlement issues that often accompany traditional fill materials, thus ensuring efficient and effective project outcomes.
Expansion Material
Expansion Material
Expansion joint material is essential for managing the natural expansion and contraction of concrete slabs, allowing movement without causing damaging forces to the slab or surrounding structures. This function is vital in areas subject to temperature fluctuations, commonly seen in applications such as concrete driveways, patios, garage slabs, sidewalks, stairways, and light pole bases.
There is a wide array of expansion joint materials available, each designed to meet specific structural and environmental needs. These materials vary in their properties, offering different advantages and disadvantages tailored to the installation’s specific requirements. Choosing the right expansion joint material is crucial for maintaining the integrity and longevity of concrete structures, ensuring both safety and durability.
Fiber Reinforcement
Fiber Reinforcement
Concrete is relatively brittle, with its tensile strength typically about one-tenth of its compressive strength. To compensate for this, reinforcement is essential. Fiber reinforcement primarily serves to enhance the concrete’s energy absorption capacity and boost its tensile and flexural strength.
There are several types of fiber reinforcements available—steel, plastic, and glass, with steel being the most commonly used. Fibers, available in various shapes and sizes, do not prevent the initial crack in concrete but significantly slow down the propagation of cracks. Incorporating fiber reinforcement can enhance the toughness of concrete by 15-30%.
Fly Ash
Fly Ash
Fly Ash is an environmentally friendly addition to concrete that helps reduce carbon emissions associated with Portland cement production. As a byproduct of coal combustion, similar to volcanic ash, Fly Ash contributes to more durable infrastructure that requires less frequent rebuilding. Many concrete mixes incorporate up to 25% Fly Ash, though it’s possible to replace even more.
Using Fly Ash in concrete offers multiple benefits: it increases strength, decreases permeability, enhances durability, and reduces both the heat of hydration (leading to less cracking) and efflorescence. Additionally, Fly Ash-enhanced concrete is more resistant to acid and fire. The final color of concrete containing Fly Ash typically varies from dark grey to yellowish tan.
Integral Color
Integral Color
Integral color is an excellent option for those looking to move beyond the traditional gray shade of concrete. By incorporating color directly into the concrete mix, integral color ensures that the hue is consistent and enduring throughout the material. This method guarantees that the color remains vibrant and unaffected by wear and tear, providing a permanent and aesthetically pleasing appearance.
Whether the concrete will be polished or left in its natural state, the color will maintain its integrity. Integral color can be applied to concrete in any setting, enhancing both indoor and outdoor spaces with a distinct color choice. This versatility makes it ideal for adding a unique touch to floors, walls, and architectural details, ensuring lasting visual impact wherever it’s used.
Rock
Rock
Coarse aggregates are rocks larger than 4.75mm, with 20mm being the most commonly used size in construction. These aggregates are vital for preparing concrete, significantly influencing the concrete’s performance characteristics such as frost resistance, permeability resistance, drying shrinkage, and overall durability.
Aggregates can be categorized into three main rock types: sedimentary, igneous, and metamorphic. Metamorphic rocks are generally not used in concrete. Among sedimentary rocks, limestone is the most frequently used in concrete due to its compatibility and performance benefits.
In contrast, igneous rocks are prevalent in concrete construction, including coarse-grained granite, basalt, andesite, and diabase. Andesite, a dark gray rock, and diabase, which has a distinctive green color and forms from the solidification of volcanic magma under deep geological conditions, are particularly valued for their robustness and are commonly utilized as aggregates in concrete.
Seasonal Warm Water Ice
Seasonal Warm Water Ice
During the cold winter months, we ensure the concrete cures consistently by providing warm water. This prevents the curing process from slowing down, which is crucial before the freezing temperatures set in at sunset. In the intense heat of summer, we use ice to maintain an even curing rate. This approach prevents the top of the concrete from curing faster than the bottom, which can lead to structural issues later on.
Washout Base Materials
Washout Base Materials
After the concrete pour is completed, it’s crucial to wash out the chutes of ready mix concrete trucks and the hoppers of concrete pump trucks to prevent any remaining concrete from hardening. Similarly, all equipment used during the pour, including wheelbarrows, shovels, and hand tools, must also be thoroughly cleaned. To facilitate this process efficiently on-site, we provide washout base materials that ensure easy and effective cleanup.